Effiziente Schweißverfahren
Qualitätsmanagement
Die Kenntnis der unterschiedlichen Verfahren und deren Entwicklung ist für die Auswahl des richtigen Schweißprozesses unerlässlich. Vor allem Hochleistungsprozesse und neue Verfahrenskombinationen eröffnen neue Dimensionen in der Fertigung, deren Potenzial sich auf die gesamte Fertigungsumgebung auswirken kann. Dabei ist es wichtig zu erkennen, dass das Bauteil und die Anwendung in vielen Fällen den Rahmen für das geeignetste Schweißverfahren vorgeben. Flexible Fertigungslösungen gewährleisten sowohl großen Unternehmen, als auch den kleinen und mittelständischen Unternehmen die Wirtschaftlichkeit.
PRAXIS – Schweißen
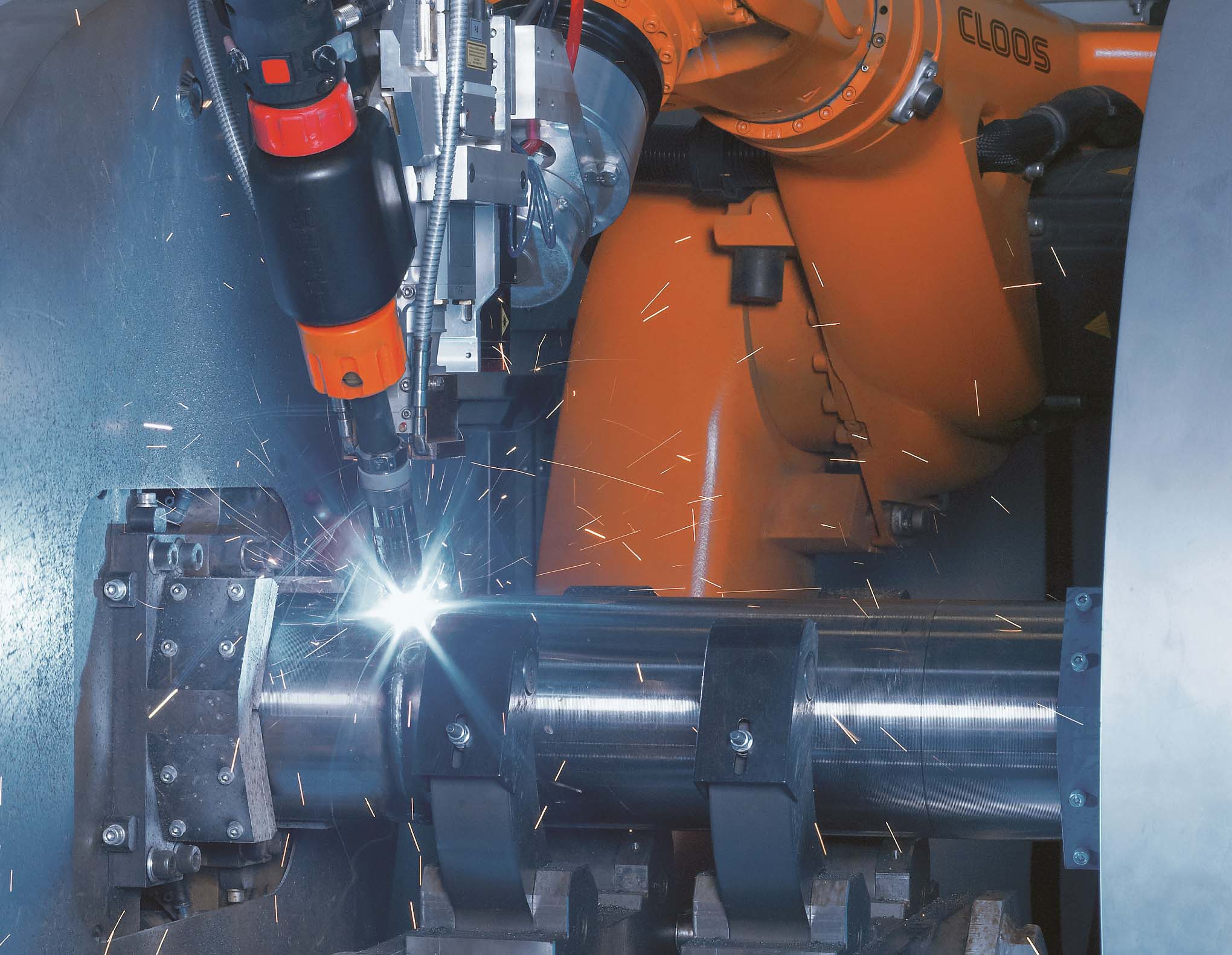
MoTion Control Weld ist ein geregelter Kurzlichtbogen mit reversierendem Drahtvorschub. Fotos: Cloos
Zu den effizienten Schweißverfahren zählen die Laserverfahren. Grundsätzlich kann der Anwender beim Verbindungsschweißen zwischen den beiden Verfahrensvarianten Wärmeleitschweißen und Tiefschweißen wählen.
In der Regel hängt die Auswahl der richtigen Technologie von der Materialdicke, dem Grundwerkstoff oder der Leistung ab. Das Wärmeleitschweißen ist mit dem Wolfram-Inertgas-Schweißen (WIG-Schweißen) vergleichbar. Der Lichtbogen schmilzt das Material lokal auf und die Kanten verbinden sich in der Schmelze zu einer sauberen, nahezu spritzerfreien Schweißnaht.
Im Vergleich zu einer WIG-Schweißnaht ist zum einen die Wärmeeinflusszone deutlich schmaler. Zum anderen sind erheblich höhere Schweißgeschwindigkeiten möglich. Dadurch kann die eingebrachte Wärme, also die Streckenenergie, deutlich reduziert werden. Dies ist insbesondere bei sensiblen Werkstoffen oder in Bezug auf thermische Verformung ein bedeutender Vorteil. Wahlweise kann dieses Verfahren mit oder ohne Zusatzwerkstoff eingesetzt werden. Je nach Material ist es empfehlenswert, wie beim WIG-Schweißen mit zusätzlichem Schutzgas oder Wurzelschutz zu arbeiten.
- Stromverlauf beim Pulsschweißen.
- Makroschliff eines einseitig von rechts geschweißten T-Stoßes mit Öffnungswinkel von 30 Grad Celsius.
- Tandem-Roboter-Kompaktanlage zur Fertigung von Kegelträgern für Schiffsantriebe.
Für größere Materialdicken ist das Tiefschweißen eine effiziente Alternative. Bei dieser Variante des Laserschweißens trifft der Laserstrahl mit hoher Energiedichte auf die Werkstückoberfläche. Der Werkstoff wird lokal aufgeschmolzen und verdampft teilweise. Dadurch bildet sich in der flüssigen Schmelze eine Dampfkapillare, das sogenannte Keyhole, das durch den entstehenden Metallplasmadruck aufrecht gehalten wird. Im Inneren wird das Licht des Lasers mehrfach reflektiert und teilweise absorbiert, wodurch das Keyhole tiefer in das Material eindringt. Durch die Vorschubgeschwindigkeit des Laserstrahls wird es durch das Material getrieben. Hinter dem Keyhole verschmelzen die beiden Kanten und es entsteht eine schmale Schweißnaht.
Das Verfahren ist gut mit einem Standard-MSG-Prozess kombinierbar. Diese Verfahrenskombination ist das Laserstrahl-MSG-Hybrid-Verfahren. Abhängig vom eingesetzten Laser, der eingebrachten Laserleistung und dem Werkstoff können Blechdicken bis zu 20 Millimetern in einer Lage geschweißt werden. Als Faustformel für einen Standardbaustahl gilt, dass für jeden Millimeter Einschweißtiefe eine Laserleistung von etwa einem Kilowatt benötigt wird.
Dadurch entfällt die bei konventionellen Schweißverfahren erforderliche Nahtvorbereitung in V-Fugenform. Dies hat eine erhebliche Einsparung bei der Nahtvorbereitung, bei der Anzahl der zu schweißenden Lagen, beim eingebrachten Zusatzwerkstoffes und bei der erforderlichen Schweißzeit. Hinzu kommt die deutlich höhere Schweißgeschwindigkeit, die beim Laserschweißen bis zu fünfmal höher sein kann als bei vergleichbaren MSG-Schweißungen.
Die hohe Schweißgeschwindigkeit hat zudem den Vorteil, dass weniger Wärme in das Bauteil eingebracht wird. Zusammen mit deutlich kleineren Nahtvolumen aufgrund der schmalen Nahtvorbereitung entsteht deutlich weniger Verzug als bei vergleichbaren MSG-Schweißungen. Dadurch ist der Aufwand für Nacharbeit an laser- und laser-MSG-hybrid-geschweißten Bauteilen deutlich geringer.
Zur Steigerung der Wirtschaftlichkeit dieses Verfahrens können weitere Verfahren miteinander kombiniert werden. Denkbar ist zum Beispiel die Kombination des Laser-MSG-Hybrid-Verfahrens mit einem zusätzlich Tandembrenner. Hierbei erzeugt der Laser-Hybrid-Kopf den nötigen tiefen Einbrand und der Tandembrenner füllt mit hoher Abschmelzleistung die Fuge vollständig auf.
Sensoren unterstützen Robotereinsatz
Die meisten modernen Schweißverfahren können sowohl manuell als auch automatisiert eingesetzt werden. Die Hochleistungsverfahren jedoch sind oft nur mechanisiert einsetzbar. Unabhängig davon können die Verfahren erst mechanisiert ihre vollen Stärken ausreizen. Die hohen Drahtvorschub- und Schweißgeschwindigkeiten können von einem Handschweißer nicht mehr erreicht werden. Aufgrund der hohen Flexibilität der modernen Robotertechnik können Robotersysteme auch für kleinere Betriebe interessant sein.
Vor allem mit Hilfe von Sensortechnik lassen sich die Fertigungsverfahren gut automatisieren. Dabei kommen unterschiedliche Sensorverfahren in Frage. Angefangen vom einfachen Lichtbogensensor, der über die Spannungsänderungen im Lichtbogen die Mitte der Fuge finden kann und somit eine Nahtverfolgung ermöglicht, über taktile Systeme, die das Bauteil berühren und somit zum Beispiel die Lage des Bauteils erkennen, bis hin zu Lasersensoren. Bei Lasersensoren unterscheidet man zwischen Offline-Sensoren, die die Naht vor dem Schweißen finden, vermessen und die programmierte Roboterbahn entsprechend korrigieren. Den Offline-Sensoren gegenüber stehen die Online-Sensoren, die dem Schweißbrenner unmittelbar vorlaufen und die Fuge abtasten. Sie können so nicht nur die genaue Position der Fuge ermitteln und so wie die Offline-Sensoren die Roboterbahn korrigieren. Online-Sensoren sind auch in der Lage, die Fugengeometrie zu vermessen und dafür zu sorgen, dass die Schweißparameter während des Schweißens an die sich ändernde Geometrien der Fuge angepasst werden. Zieht sich zum Beispiel eine Fuge im Verlauf der Schweißung immer weiter zu, können die Schweißgeschwindigkeit oder Leistung verändert werden, um eine unzulässige Nahtüberhöhung zu vermeiden.
Von einfachen Mechanisierungslösungen bis hin zu komplexen Roboterlösungen: flexible Fertigungssysteme und intelligent ausgewählte Schweißverfahren verkürzen die Durchlaufzeit zu schweißender Produkte. Zudem können ganzheitliche Lösungen zur Mechanisierung und Automatisierung sowie modulare Automatisierungslösungen mit Anpassungsfähigkeit an wechselnde Aufgaben erhebliche Kosten sparen und die Fertigungsqualität verbessern. Stets muss der gesamte Fertigungsprozess berücksichtigt werden.
Jan P. Pitzer
Gruppenleiter Anwendungstechnik
Carl Cloos Schweißtechnik GmbH
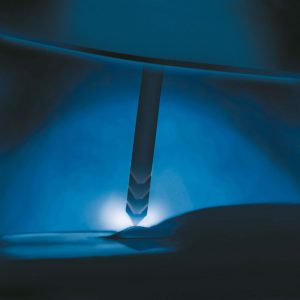
MoTion Control Weld ist ein geregelter Kurzlichtbogen mit reversierendem Drahtvorschub.
Zusatzinformation
Das Cloos-Produktspektrum reicht von einfachen, kompakten Systemen bis hin zu komplexen, verketteten Anlagen mit selbstständiger Bauteilidentifizierung und automatischen Be- und Entladeprozessen. Mit dem neuen Gateway von Cloos kann der Kunde Daten nach seinem Bedarf managen. In dem ganzheitlichen Informations- und Kommunikationstool werden sämtliche Daten zentral erfasst und verarbeitet.
Die anwenderspezifische Darstellung der Informationen ermöglicht eine detaillierte Visualisierung, Auswertung und Weiterverarbeitung der gesammelten Daten. Das neue System besteht sowohl aus der anlagennahen Hardware als auch aus diversen Softwaremodulen. Im ersten Schritt wird das Modul „Anlageneffizienz“ vorgestellt. Damit können Anwender die Performance und Wirtschaftlichkeit ihrer Roboteranlagen darstellen, Engpässe lokalisieren und die Effizienz steigern.
„Auch in der Schweißtechnik bietet die Digitalisierung erhebliches Potenzial, um Wirtschaftlichkeit und Qualität zu verbessern“, erklärt Cloos-Geschäftsführer Sieghard Thomas. „Gefragt sind innovative Lösungen, bei denen die einzelnen Komponenten einer Schweißanlage und übergeordnete Systeme bidirektional miteinander vernetzt sind.“