KI-gestützte Schnittkantenoptimierung beim Blechschneiden mit Trumpf
Software zur Qualitätssicherung
Im Lab »Flexible Blechfertigung« haben Fraunhofer IPA und Trumpf eine KI-basierte Lösung entwickelt, um Maschinenparameter beim Laserschneiden automatisiert zu optimieren. Die Methode verbessert die Schnittkantenqualität, senkt Produktionskosten und reduziert Ausschuss – auch bei variierenden Materialgüten.
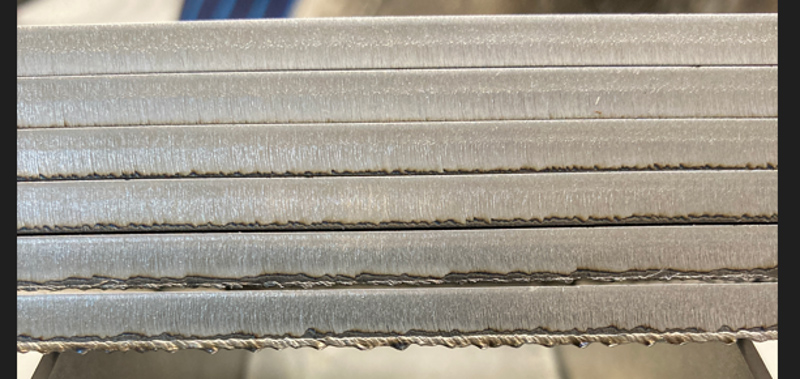
Mit den Standardparametern (unten) entsteht ein sehr großer Grat, dieser reduziert sich schrittweise und erreicht nach fünf Iterationen eine ideale Qualität (Bild: Trumpf)
Das Fraunhofer-Institut für Produktionstechnik und Automatisierung IPA hat gemeinsam mit der Firma Trumpf im Lab »Flexible Blechfertigung« eine innovative Lösung zur automatisierten Optimierung von Maschinenparametern beim Laserschneiden von Blechen vorgestellt. Durch den Einsatz von Künstlicher Intelligenz (KI) lassen sich die Einstellungen von Laserflachbettmaschinen automatisiert und effizient anpassen – insbesondere bei variierenden Materialgüten oder Materialschwankungen.
Traditionell werden diese Parameter manuell durch Fachkräfte eingestellt. Das erfordert nicht nur Zeit, sondern birgt auch die Gefahr von Ineffizienzen, da die Maschinen möglicherweise über längere Zeit nicht optimal konfiguriert laufen. Die manuelle Vorgehensweise hängt stark von individueller Erfahrung ab und kann durch komplexe Prozesszusammenhänge zusätzlich erschwert werden.
Transfer-Learning-Ansätze
Der nun entwickelte KI-Algorithmus nutzt vorhandene Maschinendaten und setzt auf sogenannte Transfer-Learning-Ansätze. So werden bereits gesammelte Erfahrungswerte in die Optimierung einbezogen, um neue Parameterkonfigurationen schnell und mit minimalem Aufwand zu finden. Dies reduziert die Anzahl der nötigen Iterationen erheblich. Philipp Wagner, wissenschaftlicher Mitarbeiter am Fraunhofer IPA, erläutert: »Unserem entwickelten KI-Algorithmus gelingt es, Vorwissen aus bereits gesammelten Daten optimal zu nutzen. Gleichzeitig schlägt er auch schnell neue Parameterkonfigurationen vor, die die Produktqualität im Vergleich zur manuellen Einstellung deutlich steigern können.«
Die Lösung wurde direkt bei Trumpf unter realen Bedingungen getestet – konkret beim Laserschneiden auf einer Laserflachbettmaschine. Die Ergebnisse zeigen, dass die neue Methode nicht nur die Schnittkantenqualität verbessert, sondern auch die Maschinenbedienung vereinfacht und Produktionskosten senkt. Zudem sinkt die Ausschussquote, was zur Erreichung von Nachhaltigkeitszielen beiträgt.
Ein zusätzlicher Vorteil: Die Beurteilung der Schnittkantenqualität kann ebenfalls automatisiert erfolgen – anhand einer schnellen Bildaufnahme und einer KI-gestützten Auswertung. Diese Analyse kann sich dabei auch an Normkriterien wie der DIN EN ISO 9013 orientieren.
Trumpf hebt hervor, dass durch die neue Lösung eine Optimierung direkt am realen Kundenteil möglich ist. Es ist nicht mehr notwendig, separate Testteile herzustellen, was Material einspart und den Prozess verschlankt. Philipp Leube von Trumpf betont: »Durch unser neues Produkt kann die Optimierung direkt am Kundenteil erfolgen. Dies erspart die Optimierung an Testteilen, für die Material extra freigehalten oder zusätzlich aufgelegt und anschließend entsorgt werden muss.«
Perspektivisch sieht das Forschungsteam Einsatzmöglichkeiten über das Laserschneiden hinaus – etwa beim Spritzgießen, der automatisierten Kabelbaummontage oder der Batteriezellenproduktion. Damit zeigt sich die Lösung als ein vielseitig einsetzbares Werkzeug für unterschiedliche industrielle Anwendungen mit hoher Variantenvielfalt.