Grüne Fertigungstechnologie für Batteriezellen
Software
In der Welt der Elektrofahrzeuge ist die effiziente und qualitativ hochwertige Fertigung von Batteriezellen in zylindrischer, prismatischer Form oder als Pouch von entscheidender Bedeutung. Gefragt sind Produktionsmethoden, die nicht nur schnell und zuverlässig sind, sondern auch umweltfreundlich arbeiten und zukünftig auch mit Recycling-Materialien zurechtkommen. Wenn es gilt, in einer kostengünstigen Massenfertigung perfekt leitende elektrische Verbindungen auch zwischen unterschiedlichen Materialien herzustellen, sind Ultraschallfügeverfahren eine gute Wahl. Das Ultraschallschweißverfahren »Soniqtwist« von Telsonic hilft, die Pole der zylindrischen Batteriezellen zu verschweißen.
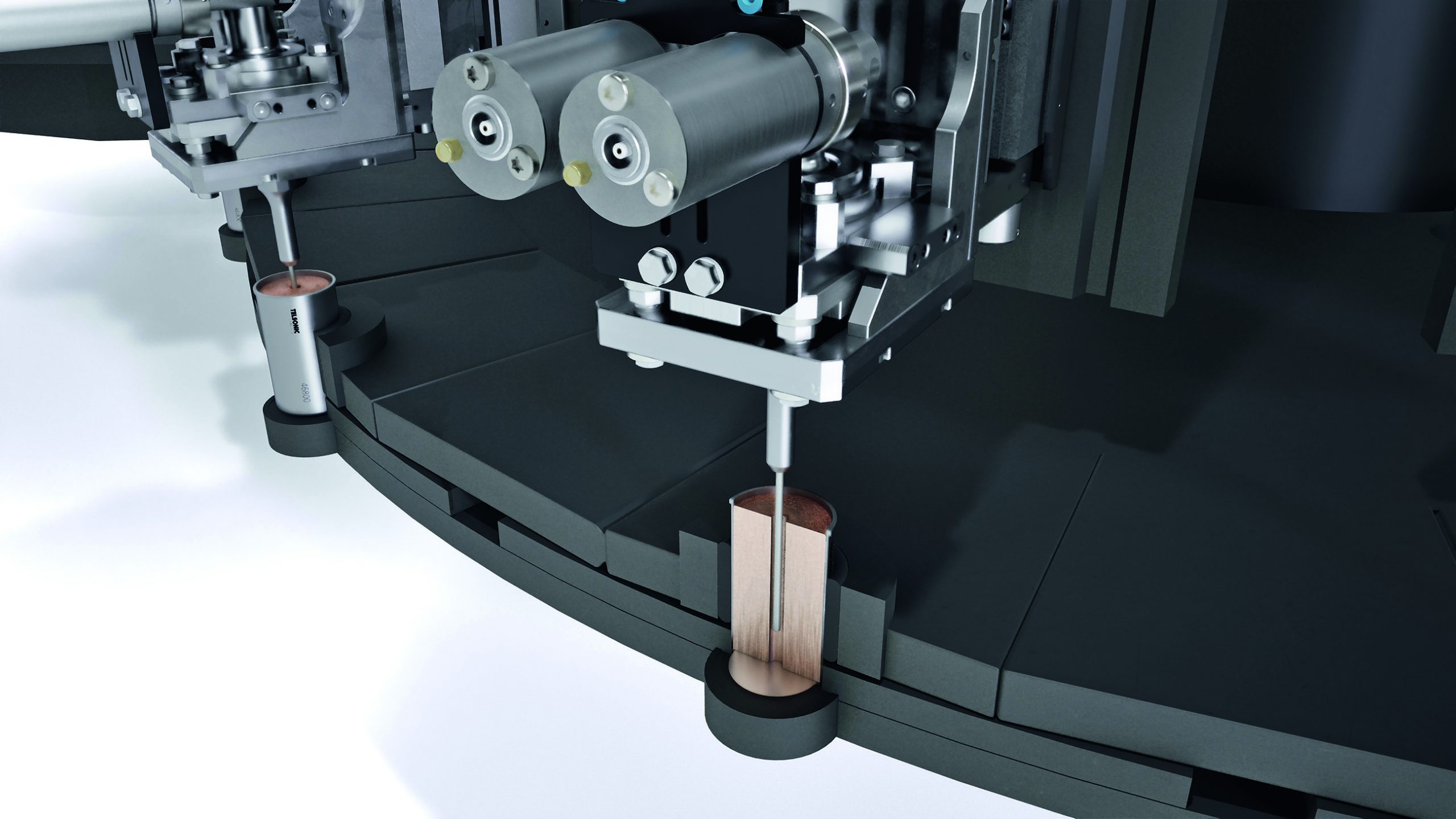
Torsionale Ultraschall-Schweißsysteme haben sich in vielen unterschiedlichen industriellen Bereichen bewährt und lassen sich einfach in Produktionsanlagen integrieren (Bilder: Telsonic).
In der Welt der Elektrofahrzeuge ist die effiziente und qualitativ hochwertige Fertigung von Batteriezellen in zylindrischer, prismatischer Form oder als Pouch von entscheidender Bedeutung. Gefragt sind Produktionsmethoden, die nicht nur schnell und zuverlässig sind, sondern auch umweltfreundlich arbeiten und zukünftig auch mit Recycling-Materialien zurechtkommen. Wenn es gilt, in einer kostengünstigen Massenfertigung perfekt leitende elektrische Verbindungen auch zwischen unterschiedlichen Materialien herzustellen, sind Ultraschallfügeverfahren eine gute Wahl. Das Ultraschallschweißverfahren »Soniqtwist« von Telsonic hilft, die Pole der zylindrischen Batteriezellen zu verschweißen.
Die Automobilindustrie favorisiert zunehmend zylindrische Akkuzellen. Sie bieten eine hohe Energiedichte, sind mechanisch robust, langlebig und lassen sich vergleichsweise einfach produzieren und skalieren: Folien aus Aluminium und Kupfer, getrennt durch eine Separatorlage, werden in vollautomatisierten Produktionslinien aufgerollt, mit elektrischen Kontaktierungen ausgestattet und in einer zylindrischen Zelle verpackt.
Die Batterie für ein durchschnittliches Elektroauto enthält je nach Leistung 1000 bis 9000 solcher Zellen, was eine hocheffiziente Produktionsmethode unabdingbar macht, um Qualität, Konsistenz und die benötigten hohen Stückzahlen zu gewährleisten. Das torsionale Ultraschallschweißverfahren »Soniqtwist« hat die Voraussetzungen für diesen Schweißvorgang. Das Verfahren hat sich bereits in unterschiedlichen industriellen Bereichen bewährt. Die Systeme lassen sich einfach und kostenminimiert in verschiedene Produktionsanlagen voll integrieren. Beispiele gibt es für Rund- und Ringtaktanlagen ebenso wie in Continous-Mode- oder Lineartaktanlagen.
Praktische Vorteile
Heutige zylindrische Batteriezellen bestehen in der Regel aus je einer zwölf Mikrometer starken Aluminiumfolie und einer acht Mikrometer starken Kupferfolie, getrennt durch eine dünne, laminierte Separatorlage. Diese Sandwich-Struktur wird dann zu der so genannten »Jelly Roll« aufgewickelt und in zylindrische Gehäuse eingebracht. Anschließend wird ein Kollektor aus Aluminium aufgeschweißt.
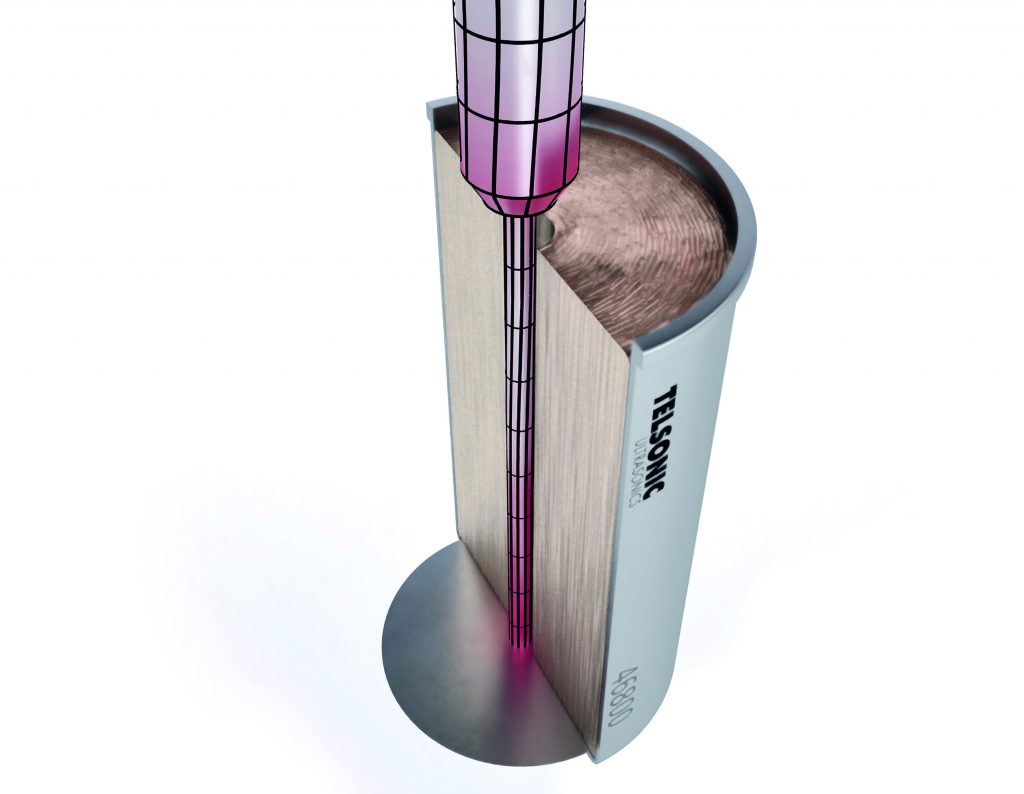
Die stabförmige Sonotrode taucht bis 160 Millimeter tief in die Jelly Roll ein. Die verschweißte Pol-Fläche hat je nach Batteriezellenausführung einen Durchmesser von zwei bis sechs Millimetern.
Dazu wird über eine hochfrequente torsionale Schweißbewegung mit einer Frequenz von üblicherweise 20 Kilohertz die »Jelly Roll« über die Aluscheibe, also den Kollektor, der die Folien verbindet, mit der Kathode (dem Pluspol) verbunden. Die stabförmige Sonotrode mit einem Durchmesser von zwei bis sechs Millimetern taucht 70 bis 160 Millimeter in die »Jelly Roll« ein und verschweißt die Aluscheibe mit dem isolierten Boden des Gehäuses.
Danach wird die Zelle mit einem Deckel verschlossen und über eine Öffnung mit Elektrolyt befüllt. Nach dem Zellfinishing, bestehend aus Formierung, Entgasen und Reifung, ist die Zelle geladen. Die Parameter für das Finishing sind je nach Zellhersteller unterschiedlich und beeinflussen in einem hohen Maß die Performance der Zelle.
Im Vergleich zur Lasertechnik, die zwar in puncto Präzision ebenfalls überzeugt, aber bei der Integration in die High-Speed-Produktionsumgebung, Produktivität und Kosten jedoch an ihre Grenzen stößt, bietet die Ultraschalltechnik gleich mehrere Vorteile: So ermöglicht das torsionale Ultraschallschweißverfahren – abhängig von der Fertigungsanlage – eine Produktivität bis zu 400 »Parts per Minute« (ppm) mit Schweißzeiten unter 300 Millisekunden. Einer effizienten Massenproduktion steht damit nichts im Wege.
Umweltfreundlich und ohne Nebenwirkung
Gleichzeitig ist das Verfahren tolerant gegenüber den eingesetzten Materialien: Batteriehersteller haben sich auf die Fahne geschrieben, möglichst grüne Batterien mit geringem CO2-Abdruck, fossilfreier Energie und einem innovativen Kreislaufsystem herzustellen. Themen wie das Batterie-Recycling sind dabei essenziell. Hier kann die Ultraschallschweißtechnik ebenfalls überzeugen, denn auch Recycling-Werkstoffe lassen sich verarbeiten.
Lasertechnik ist für letztere beispielsweise nicht geeignet, weil darin oft Stoffe enthalten sind, die den Laserstrahl reflektieren und damit das Schweißergebnis negativ beeinflussen. Im Gegensatz zu anderen Schmelzschweißverfahren minimiert die Ultraschallmethode durch die geringe Wärmeentwicklung, die 30 bis 40 Prozent unter dem Schmelzpunkt liegt, auch das Risiko von Porenbildung, Spritzern und Heißrissen. Poren in den Polverbindungen könnten beispielsweise im späteren Betrieb bei Vibrationen zu Rissen und damit zu Ausfällen führen.
Ultraschallschweißsysteme verbrauchen zudem nur wenig Energie, da die Systeme mit minimalem Energieaufwand im Resonanzpunkt arbeiten; im Vergleich zu anderen Fügeverfahren spart das viel Energie. Ultraschallschweißen erfordert zudem keine Schutzausrüstung, verursacht keine gefährlichen Emissionen oder Abfälle und benötigt keine Zusatzwerkstoffe wie Flussmittel oder Lote. Diese Aspekte sind im Einklang mit den Umweltzielen der E-Mobilität und machen torsionales Ultraschallschweißen zu einer zukunftsweisenden grünen Technologie in der Batteriezellenproduktion für Elektrofahrzeuge. Es unterstützt Nachhaltigkeitsziele und verbessert das Firmenimage.
Produktionsqualität im Blick
Da Nachhaltigkeit eng mit Produktionsqualität und Fehlervermeidung verbunden ist, setzt Telsonic auf eine digitale Plattform, die eine nahtlose Integration und Steuerung von Ultraschallkomponenten von der Labor- bis zur Serienanlage ermöglicht. Mit »TelsoAssist« werden die einzelnen Ultraschallkomponenten digital zu einem Gesamtsystem verbunden.
Die Einbindung der Sensorik ermöglicht präzise Messungen wichtiger Parameter und korrekte Prozessregelung. Die Software unterstützt in allen Phasen eines Projekts, von der Anwendungsentwicklung im Labor über die Integration, Inbetriebnahme, Produktion bis hin zum Service und Support.
Durch konsequent genutzte, software-gestützte Dokumentation stehen maschinenlesbare Echtzeitdaten zur Verfügung, um Prozesse zu überwachen, Trends zu erkennen, die Qualität sicherzustellen und fortlaufend zu optimieren. Self-Check-Funktionen der eingesetzten Werkzeuge, eine bildunterstützende Menüführung für den Bediener, einfache Visualisierung, Wartungszähler für Verschleißteile und Equipment-Management sowie Barcodeleser stellen sicher, dass für jede Applikation die passenden Werkzeuge mit validierter Parametrierung eingesetzt werden und dienen einer konsequenten Fehlervermeidung.
Die perfekt aufeinander abgestimmte Lösung aus Software und Hardware, intuitive Dashboards und der netzwerkübergreifende Datenaustausch über verschiedene Schnittstellen wie Profinet, EtherNet/IP, EtherCat und Powerlink bieten Transparenz und Effizienz in der Produktion und ermöglichen den Aufbau von KI-Funktionalitäten.
Der Technikkasten
Das torsionale Ultraschallschweißverfahren »Soniqtwist« ist ein hochfrequentes Reibschweißverfahren. Die Sonotrode führt abwechselnd torsionale Bewegungen um die Längsachse in die eine und andere Richtung durch. Dabei wird in kurzen Zeiten (zwischen 0,1 und 0,4 s) mit einer Frequenz von 20 Kilohertz und Amplituden bis 50 Mikrometern in die Grenzfläche der beiden Teile eingebracht.
Gleichzeitig sorgt die torsionale Bewegung der Sonotrode dafür, dass die Umgebung der Schweißzone durch den Ultraschall praktisch nicht belastet wird. Leistungen bis zu 14,4 Kilowatt können mit dem Verfahren übertragen werden. So lassen sich auch bei schwierigen Materialkombinationen hohe Festigkeiten bei großen Schweißflächen erzielen. Abzugsfestigkeiten von einigen 100 Newton pro Quadratmillimeter sind möglich, je nach Bauteil und Anforderungsprofil.