Höchste Präzision beim Schweißen
Machine Vision
Die Unternehmen DataVision und MVTec haben eine Plattform für maschinelles Lernen entwickelt, bei der eine Cloud-Lösung in Kombination mit industrieller Bildverarbeitungssoftware für erhebliche Effizienzsteigerungen sowohl in der Entwicklung als auch in der Produktion sorgt. Eine Anwendung, die auf dieser Kombination fußt, wurde von der Sick AG bei Škoda Auto in der Tschechischen Republik erfolgreich implementiert.
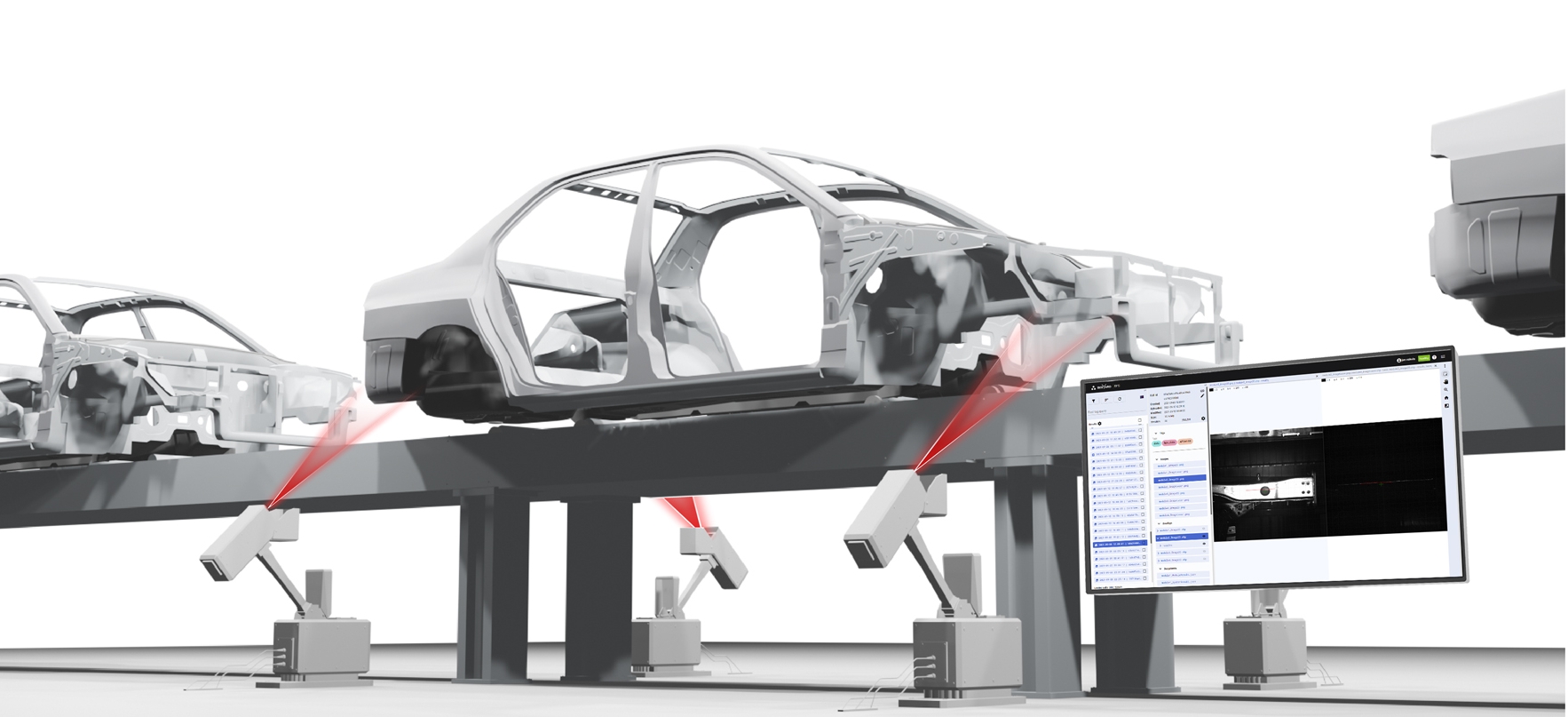
Mit Unterstützung der MVTec Software GmbH hat DataVision s.r.o. »BeeYard« entwickelt, eine cloud-basierende Machine-Learning- und Datamanagement-Plattform, die die Vorteile der industriellen Bildverarbeitung (Machine Vision) mit denen der Cloud verbindet. »Auf der einen Seite können Entwicklungsteams die leistungsstarke Lösung nutzen, um die Entwicklung zuverlässiger Anwendungen auf Basis zentralisierter Datensätze und Cloud-Rechenleistung zu beschleunigen«, erklärt Jaroslav Jahoda, CTO bei DataVision. »Andererseits erhalten die Endkunden eine schlüsselfertige Lösung für das Datenmanagement und die Rückverfolgbarkeit innerhalb ihrer Smart Factory. Das Zusammenspiel der Produkte beider Unternehmen bietet einen entscheidenden Mehrwert auf dem Weg zur Smart Factory.«
Hightech-Kooperation
Sick, Lösungsanbieter für sensorbasierende Anwendungen, hat für Škoda Auto eine vollautomatische Anwendung zur Positionsbestimmung realisiert. Mit »BeeYard« bietet das Unternehmen eine webbasierende Plattform für maschinelles Lernen, die von der Datenerfassung und -beschriftung über die Algorithmenentwicklung bis hin zum MLOps-Workflow Unterstützung bietet.
Positionserkennung durch Machine Vision
Das Herzstück der Anwendung ist ein Body Positioning System. Das auf Machine Vision basierende System wird direkt an den Produktionslinien in den Schweißereien von Škoda eingesetzt. Das verwendete Kamerasystem besteht aus Lasern und InspectorP654 Smart 2D-Kameras von Sick.
Jede Schweißzelle verfügt über vier Messmodule, eines dient der Redundanz, die zusammen die exakte 3D-Position der Karosserie in der Fertigungslinie bestimmen. Dank der Bildverarbeitungssoftware »Halcon« von MVTec kann die Position der Karosserie zuverlässig bestimmt werden, so dass die Schweißroboter beim Punktschweißen eine Genauigkeit von plusminus einem Millimeter erreichen können. Die bisherige Anwendung war teuer und anfällig für mechanische Schäden und hatte hohe Wartungskosten. Darüber hinaus war der gesamte Prozess nicht effizient, da die Karosserie mechanisch angehoben werden musste, was Produktionszeit kostete.
Zuverlässige Lösungen
Das Body Positioning System basiert auf Algorithmen, die mit der Bildverarbeitungssoftware entwickelt wurden. Es vermisst kontinuierlich Karosserien in der Produktionslinie und speichert die Messwerte. So kann im Falle einer Produktionsänderung, zum Beispiel bei einem neuen Karosserietyp, die interaktive BPS-Webschnittstelle diese Änderung problemlos verarbeiten.
Wenn eine neue Funktionalität hinzugefügt werden muss, stellt »BeeYard« die richtigen Werkzeuge zur Verfügung, um die Leistung des neuen Algorithmus zu bewerten und die Leistung zu demonstrieren, bevor er in der Produktion eingesetzt wird. Dieses Verfahren gewährleistet nicht nur die langfristige Gesamtstabilität des Systems, sondern auch maximale Flexibilität.
Die »BeeYard«-Plattform ermöglicht es, Daten von verschiedenen Stationen zu einem Datensatz zusammenzuführen. »Dadurch ist es möglich, die Algorithmen nicht nur in einzelnen Schweißzellen zu testen, sondern auch standortübergreifend, sogar aus verschiedenen Produktionsstätten. Dieser tiefe Einblick in alle Produktionsdaten ermöglicht die Optimierung der Produktion, der Algorithmen und der Anlagenwartung«, sagt Jahoda.
Auf mehreren Ebenen messbar
Inzwischen ist das System seit zwei Jahren in Betrieb. »Die Anwendung hat unsere Ziele und Anforderungen in mehrfacher Hinsicht erfüllt. Da sind zum einen die Ziele Wirtschaftlichkeit, Effizienz und nicht zuletzt der Klimaschutz«, berichtet Jan Čejka, Projektkoordinator für Welding Shop Robotizations bei Škoda Auto. Konkret werden äußerst robuste Lokalisierungsraten von nahezu 100 Prozent erreicht, was zu einer fünfprozentigen Reduzierung der Taktzeiten für die einzelnen Karosserien führt.
Darüber hinaus entfallen im Vergleich zu mechanischen Lösungen der mechanische Verschleiß und die Wartung nahezu vollständig, was die Betriebskosten senkt. Schließlich kommt es zu einer deutlichen Einsparung beim Energieverbrauch, was mit einer Verbesserung der CO2-Bilanz einhergeht.
Weitere Ziele des Projekts waren die Schritte auf dem Weg zur intelligenten Fabrik. »Durch die Transformation von der mechanischen zur digitalen Lösung konnten wir nicht nur Verbesserungen erzielen, sondern auch ganz neue Anwendungsfälle realisieren und die Produktion deutlich optimieren«, freut sich Čejka. Der Einsatz der intelligenten Vernetzung von Cloud und Machine Vision erhöht die Flexibilität, indem zum Beispiel unterschiedliche Karosserietypen auf einer einzigen Produktionslinie bearbeitet werden können.
Darüber hinaus gibt es einen weiteren Punkt, der über den bloßen Übergang von einer mechanischen zu einer digitalen Lösung hinausgeht. Und zwar, dass im Rahmen der Industrie-4.0-Bemühungen eine große Menge an Daten gesammelt wird, die auch für andere Zwecke genutzt werden kann. Ein Beispiel ist die vorausschauende Wartung. Die notwendige Maschinenwartung wird nun in einem entsprechend frühen Stadium erkannt, was letztlich Maschinenstillstände verhindert.