Flexible Automatisierung in der Batteriemontage
Qualitätsmanagement
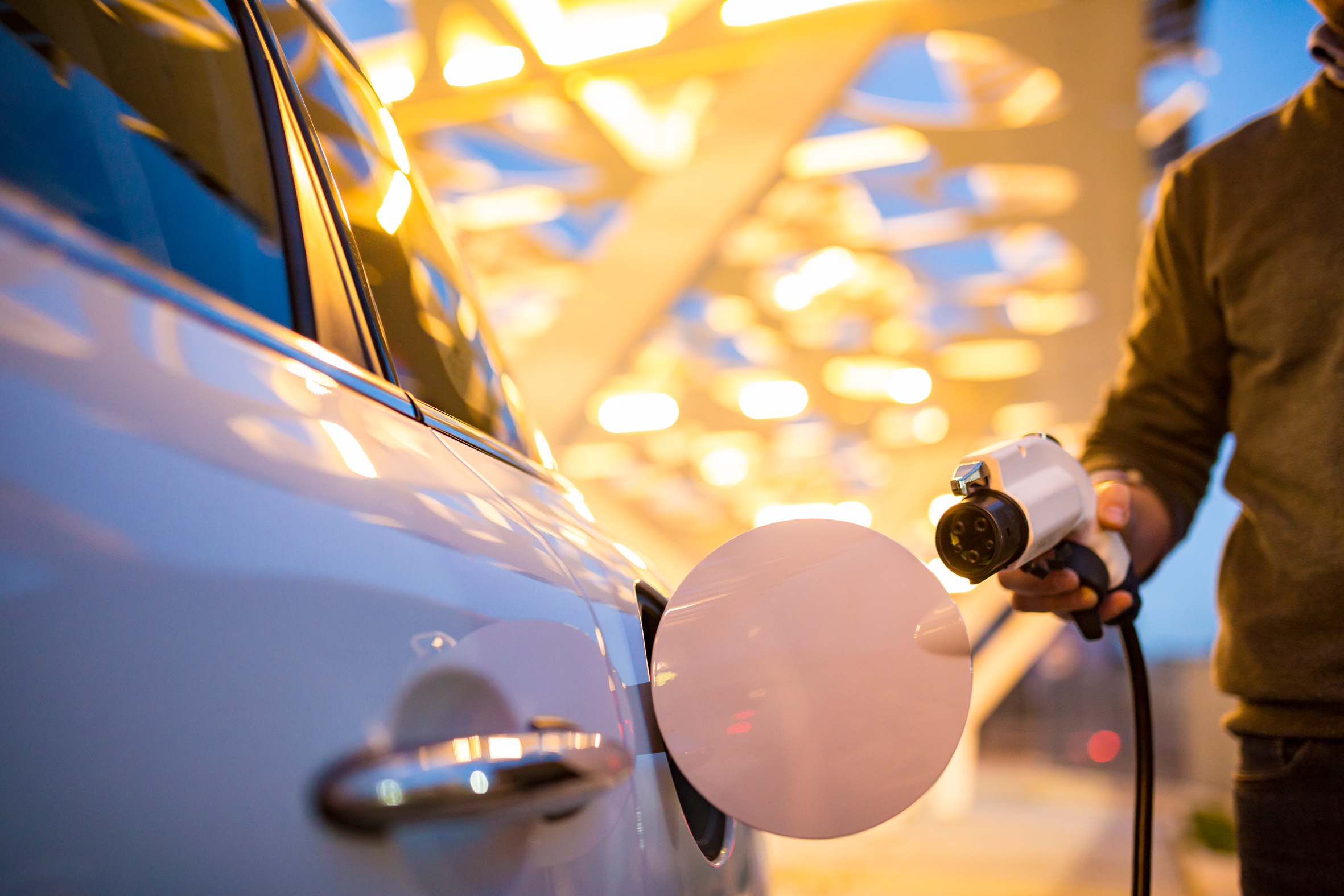
Bei Lösungen für die Fertigung alternativer Antriebe kann Liebherr auf die Erfahrungen bei Produktionslinien für Verbrennermotoren zurückgreifen. Bild: Liebherr
Lösungen für die Fertigung alternativer Antriebe sind dringend gesucht. Allerdings lassen sich die Bedingungen für die Montage von Verbrennungsmotoren nicht einfach auf die Montage von Batterie-Packs übertragen. Herausforderungen sind das Handling und die sicherheitsrelevante Behandlung von Batteriekomponenten. Liebherr kann auf die Erfahrungen bei Produktionslinien für den Verbrennungsmotor zurückgreifen. Der Unterschied liegt darin, dass es sich um ein Werkstück handelt, das auch sehr unterschiedlichen Montage- und Technologieprozessen unterliegt.
Für den technologischen Wandel in der Automobilindustrie hin zu alternativen Antrieben hat Liebherr eine modulare Automatisierungslösung zur Montage von Batterie-Packs entwickelt – von der Kleinserienfertigung bis zur vollautomatisierten Volumenproduktion. Vorteile für die Anwender sind die Systemfähigkeit und Prozesssicherheit, schnelle Taktzeiten und Flexibilität.
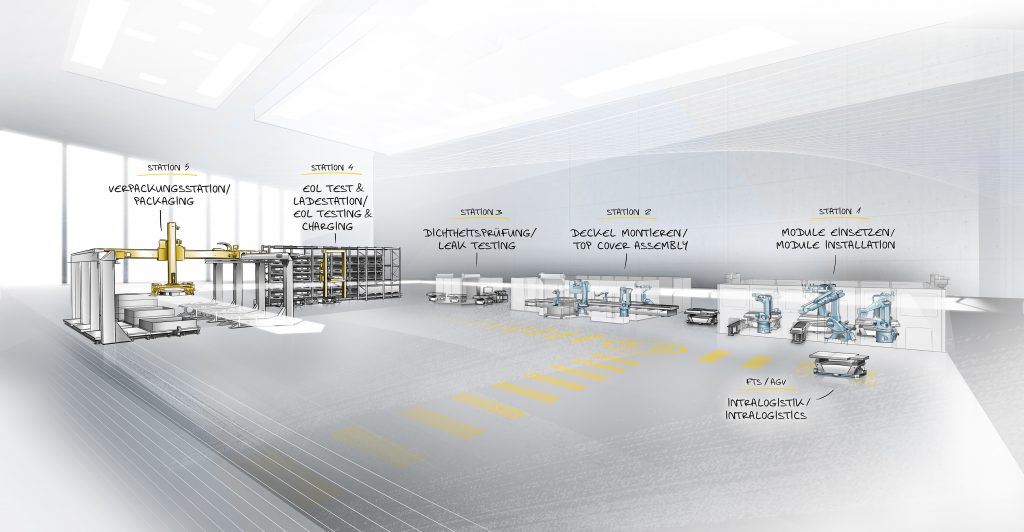
Überblick: Die modulare Automatisierungslösung für die Montage von Batterie-Packs reicht von der Kleinserienfertigung bis zur vollautomatisierten Volumenproduktion. Bild: Liebherr
Etliche Produkte aus dem eigenen Unternehmen – vom Betonmischer bis zum Mobilkran – besitzen bereits Elektroantriebe. Angesichts der prognostizierten Entwicklungen lag es nahe, das Portfolio der Automationssysteme in Bezug auf die Anforderungen, die mit der Elektrifizierung in der Automobilbranche einhergehen, unter die Lupe zu nehmen.
Ein Entwicklungsprojekt fand unter wissenschaftlicher Begleitung der KIT Campus Transfer GmbH, einer Ausgründung des Karlsruher Instituts für Technologie, und der PEM Motion GmbH, einer Ausgründung der RWTH Aachen, statt. Das Forschungsprojekt kam zu dem Ergebnis: Bisher wird noch viel manuell oder halbautomatisiert gefertigt, aber die steigende Nachfrage kann nur mit Automatisierungslösungen bedient werden. In der Serienproduktion von Komponenten für Verbrennungsmotoren ist die automatisierte Montage seit langem das Kerngeschäft der Liebherr-Automationssysteme.
Montage und Sicherheit
Die Bedingungen, die bei der Montage von Verbrennungsmotoren herrschen, lassen sich nicht eins zu eins auf die Montage von Batterien übertragen. Eine Herausforderung beim Handling von Batterie-Packs ist das Gewicht: Ein fertig montiertes Batterie-Pack im Automobilbereich wiegt bis zu 800 Kilogramm. Für diese Gewichtsklasse sind die Handlingsysteme von Liebherr geeignet.
Eine weitere Herausforderung sind die sicherheitsrelevanten Eigenschaften von Batterieteilen. Strenge Sicherheitsvorschriften gelten bei der Systemauslegung. »Dabei können wir auf die vorhandenen Erfahrungen, insbesondere bei Produktionslinien für die Automobilindustrie, zurückgreifen«, erläutert Thomas Mattern, Entwicklungsleiter Automationssysteme. Der große Unterschied liegt darin, dass es sich um ein Werkstück handelt, das unterschiedlichen Montage- und Technologieprozessen unterliegt. Darüber hinaus ergeben sich besondere Anforderungen aufgrund der Eigenschaften wie Gefahrstoffe, Brennbarkeit und elektrische Ladung. »Gerade solche Herausforderungen bieten gewisse Anreize, für die wir gut gerüstet sind«, sagt Mattern.
Systemfähigkeit und Know-how bei der Prozessintegration sind notwendig. Produktspezifische Prozessstationen wie Dosiereinheiten, Schraubstationen oder die Dichtheitsprüfung, die nicht zu den Kernkompetenzen von Liebherr zählen, werden mit geeigneten Partnern und Zulieferern gelöst und in den Gesamtprozess integriert.
Modularer Produktbaukasten
Modularität, Skalierbarkeit und Vernetzung der Komponenten spielen eine wichtige Rolle. Dem Anwender steht ein Produktbaukasten zur Verfügung: Handlingsysteme speziell für schwere Transportlasten, Linearportale für schnelle Taktgeschwindigkeiten, Industrieroboter für komplexe Aufgaben, Speicherlösungen, Intralogistik und die entsprechende Steuerung.
Mattern zieht einen Vergleich: »Das ist wie bei einem Legobaukasten. Die hohe Kunst ist es, die Bausteine individuell zusammenzusetzen. Unsere Systeme besitzen universelle Schnittstellen, quasi die Noppen der Legosteine. Daraus konfigurieren wir je nach Kundenanforderung eine ganz individuelle Anlage.« So können teilautomatisierte Anlagen für kleine Stückzahlen oder vollautomatisierte Linien für die Großserienproduktion skalierbar ausgelegt werden.
Wenn es um Schnittstellen, Parallelprozesse, Reproduzierbarkeit, Notfallstrategien, Teileverfügbarkeit und -rückverfolgung geht, wird ein erfahrener Partner benötigt. »Für die Montage von Batterie-Packs können wir von einzelnen, miteinander kombinierbaren Prozessstationen bis hin zu einer kompletten Turnkey-Anlage alles aus einer Hand liefern«, fasst Jan Pollmann, Entwicklungsingenieur Automationssysteme, zusammen.