Predictive Maintenance sinnvoll nutzen
Sensoren
Jeder Stopp der laufenden Produktion lässt die Kosten steigen. Wenn eine Maschine ausfällt, entstehen neben Reparaturkosten zusätzlich Umsatzeinbußen. Um Schäden frühzeitig zu erkennen, setzt Mitsubishi Electric auf eine intelligente Sensorlösung. Motorspindeln – das Herzstück jeder Werkzeugmaschine – sind extremen mechanischen Belastungen ausgesetzt. Bleiben Überlastungen unentdeckt, können Ausfälle die Folge sein. Diese lassen sich durch vorausschauende Wartung verhindern. Mit intelligenter Sensorik werden Defekte erkannt, bevor sie tatsächlich eintreten.
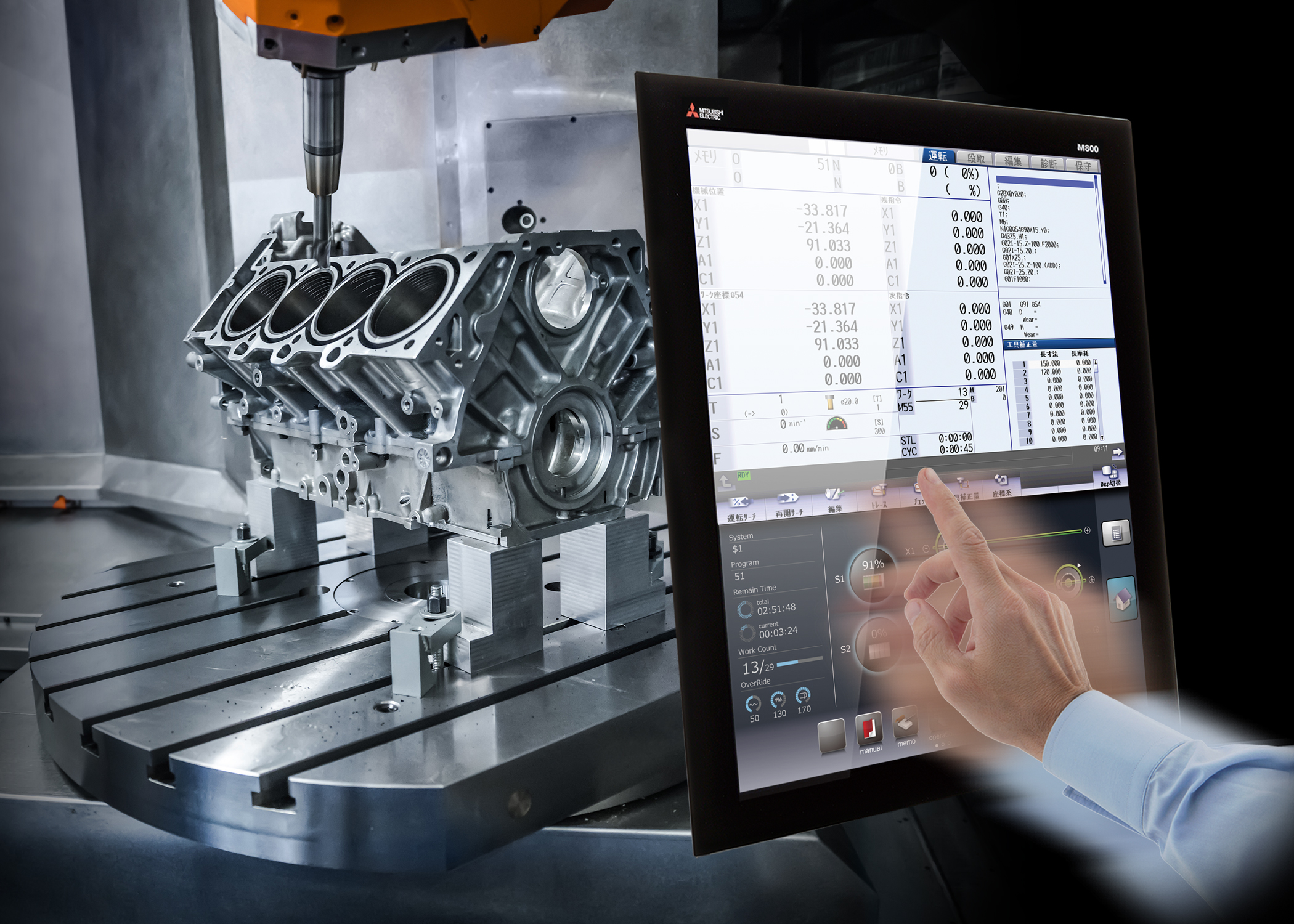
Die Predictive-Maintenance-Lösung für Werkzeugmaschinen ermöglicht die optimale Planung von Wartung und Teileaustausch. Bild: Mitsubishi
Um Spindeldaten auszuwerten, anhand derer sich die Ausfallwahrscheinlichkeit prognostizieren lässt, hat Mitsubishi Electric die i³SAAC-Sensoren von Lenord + Bauer in die Maschinensteuerung implementiert. Die MiniCODER mit integrierter digitaler Schnittstelle liefern gezielt gefilterte und optimierte Funktionen sowie Zusatzinformationen. So ist es möglich, genaue und aktuelle Statusinformationen abzurufen.
Das bewährte Messprinzip des Motorfeedbacksystems bleibt unverändert: Die MiniCODER erfassen Drehzahlen bis zu 100.000 Umdrehungen pro Minute. Somit eignen sie sich als Istwertgeber für die Spindeln und Positioniersysteme von Werkzeugmaschinen. Darüber hinaus überwachen sie Temperatur, Position sowie die Betriebsstunden und liefern Informationen für ein elektronisches Typenschild. Diese Parameter machen die Instandhaltung planbar. Die Prozessdaten werden direkt im Sensor zur Laufzeit verarbeitet und aufbereitet in Echtzeit übertragen. Das System gibt frühzeitig Warn- und Statusmeldungen aus, wenn Wartungsarbeiten anstehen oder Komponenten erneuert werden müssen.
»Reparaturen lassen sich kosteneffizient rechtzeitig dann durchführen, wenn der Werkzeugmaschine ein Leistungsverlust droht«, erklärt Frederik Gesthuysen, Manager CNC Sales Administration & Marketing, Division Mechatronics CNC bei Mitsubishi Electric.
Sensoren fangen an zu denken
Die intelligenten Sensoren basieren auf integrierten leistungsfähigen Mikrocontrollern und können auf eine umfangreiche Systemsoftware zurückgreifen. Die Protokollstacks für die digitalen Schnittstellen bilden die zentrale Basis für die realisierbaren Funktionen und Dienste.
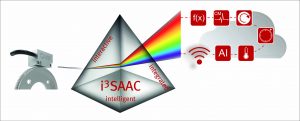
Condition Monitoring wird durch intelligente Drehzahl- und Positionssensoren unterstützt. Bild: Lenord + Bauer
Betrachtet man die Anforderungen an Motorspindeln mit typischen Drehzahlen von 10.000 bis über 50.000 Umdrehungen pro Minute genauer, so ergeben sich Protokollzeiten von wenigen Mikrosekunden. Die zertifizierten Protokollstacks garantieren im Beispiel des Highspeed Mitsubishi-Protokolls MHSSI eine Echtzeitübertragung der Drehzahlinformationen in weniger als zehn Mikrosekunden und darüber hinaus die Übertragung weiterer Zustandsdaten wie der Temperatur am Spindellager. Während der Datenübertragung werden die Drehzahldaten permanent weiter erfasst und im MiniCODER zur nächsten Übertragung aufbereitet. Auf Mikroprozessorebene müssen dazu interne Zykluszeiten von einer Mikrosekunde für die Informationen zur Laufzeit und von zehn Mikrosekunden für weitere Taskebenen sichergestellt werden.
Zukünftig werden die MiniCODER Mehrwert liefern: Interne, gefilterte und optimierte Daten werden miteinander kombiniert. So werden Messwerte mit weiteren Signalen wie Vibration oder radialer und axialer Wellenverlagerung verknüpft.
Um den Anlagenzustand beurteilen zu können, müssen gesammelte Maschinendaten mit intelligenten Algorithmen ausgewertet werden. Dieser steigenden Datendichte begegnet Lenord + Bauer mit Edge-Computing und Lösungen unterstützt durch künstliche Intelligenz. Die vorgelagerte Instanz, zum Beispiel eine zentrale Steuerung, erhält die benötigten Daten vom „Rand des Netzwerkes“ mittels serieller Protokolle zielgerichtet aufbereitet. Das begrenzt die Datenflut auf der Maschinenebene und ermöglicht weiterführende Aussagen zur vorausschauenden Wartung.
Die intelligenten Sensoren digitalisieren die Messwerte aus dem Antrieb und ermöglichen das Verknüpfen mit verschiedenen Punkten in der CNC, zum Beispiel am Frequenzumformer. Hierfür hat der Sensorspezialist die Lösung MC Observer entwickelt. Die Daten werden entweder direkt in die CNC-Steuerung übertragen oder zuvor mittels eines OPC-Servers aufbereitet.
Informationen einfacher austauschen
Wichtig ist auch der Blick über die Bedienoberfläche einer Anlage hinaus in das übergeordnete Planungs- bzw. ERP-Netzwerk. Basierend auf dem OPC-UA-Standard definiert der Verband deutscher Werkzeugmaschinen gemeinsam mit der Werkzeugmaschinenindustrie das umati-Protokoll (Universal Machine Tool Interface). Ziel ist es, die digitale Vernetzung mittels universeller, standardisierter Schnittstellen voranzutreiben. Maschinen und Automatisierungslösungen sollen sich zukünftig weltweit über eine gemeinsame Sprache miteinander abstimmen. Das reduziert den Aufwand für die Maschinenanbindung an kundenseitige IT-Infrastrukturen.
Lenord + Bauer berücksichtigt diesen Standard: Die Sensordaten können vollständig aufbereitet direkt in die einheitliche umati-Sprache transferiert werden. Der Signalpfad des Motorfeedbacksystems bleibt unangetastet und die Safety-Anforderungen werden erfüllt. Die durchgängige Systemlösung mit digitalen Schnittstellen im Motorfeedback-Sensor bedient Echtzeitanforderungen auf der Maschinenebene genauso wie OPC UA basierende Servicekommunikation auf Serverebene.
Einfache Implementierung
Die Reduzierung des Aufwands steht auch bei der Konfiguration und Einbindung der Sensoren in die Steuerung im Vordergrund. Diese wird zukünftig direkt über die Visualisierung der CNC-Steuerungsebene erfolgen. Derzeit ist die einfache Integration mithilfe eines Servicetools möglich, mit dem die analogen Sensorwerte im eingebauten Zustand auf den tatsächlichen Luftspalt zwischen MiniCODER und Messzahnrad abgeglichen werden können.
Neben der reinen Funktionsprüfung und Sensoroptimierung kann direkt ein Fingerprint des gesamten Sensorsystems aufgenommen und gespeichert werden. Mit dieser Datenbasis im MiniCODER können bei der Konfiguration Schwellwerte für die zulässigen Schwankungen um die initialen Messdaten und den Spindeltyp definiert werden. Die permanente Überwachung dieser Werte findet im Sensor zur Laufzeit ohne Belastung des Anlagenbusses beziehungsweise der CNC-Steuerung statt. Zusätzlich werden die Betriebsstunden konfigurierbar auf die Nenndrehzahl der Motorspindel unverlierbar als Drehzahlhistogramm gespeichert.
Neue Geschäftsmodelle
Die gespeicherten Systemdaten eröffnen neue Analysemöglichkeiten im Garantie- und Servicefall. Sie liefern Informationen über die tatsächlichen Arbeitsdrehzahlen und damit die Lagerbelastungen. Zudem kann der Fingerprint des Messsystems im Auslieferungszustand hinzugezogen werden. Insbesondere die OEMs der Motorspindel profitieren von der Identifikation der Ausfallursachen zur Bewertung von Garantiefällen. Darüber hinaus können sie die Felddaten zur Optimierung ihrer Produkte auswerten.
Der Spindel-Service wird häufig über Drittanbieter abgewickelt. Dank des elektronischen Typenschilds kann der richtige i³SAAC-MiniCODER automatisch erkannt werden. Der korrekte Einbau von MiniCODER und Messzahnrad wird durch den Feinabgleich im eingebauten Zustand und den Fingerprint des Systems dokumentiert.
Zudem kann der Drittanbieter einen maßgeschneiderten Wartungsservice anbieten, der auf den gesammelten Maschinendaten basiert. Wartungszyklen lassen sich präziser hervorsagen. »Mit vorausschauender Wartung lässt sich der optimale Zeitpunkt für den Tausch von Spindelkomponenten finden und in die laufende Produktion einplanen«, sagt Gesthuysen. »Im Endeffekt bedeutet das mehr Produktionszeit, geringere Reparaturkosten und einen Langzeitschutz für die Werkzeugmaschinenspindel. Durch intelligente Sensoren fließt das Expertenwissen der Sensorhersteller zur Datenanalyse in ein umfassendes Condition Monitoring ein und unterstützt die Prozessoptimierung nachhaltig.«